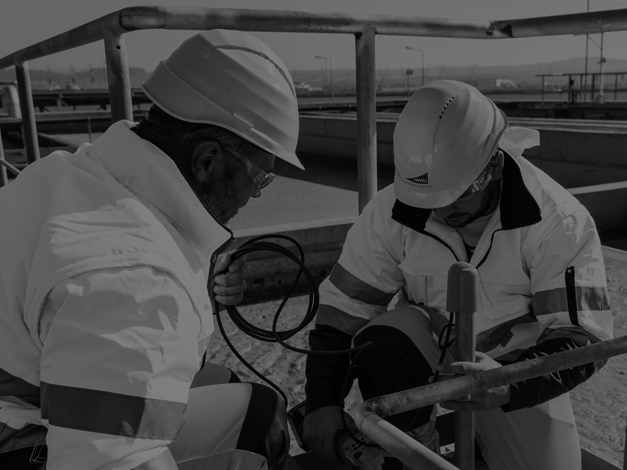
The Preferred Partner for Those Who Value Water
Wherever Ovivo touches water, we seek to add value.
We leverage our expertise and product innovation to deliver the best water treatment solutions in the world. As complete water specialists, we understand the complexities of water treatment and the day-to-day realities of our customers.
Learn MoreLatest News
Addressing EPA’s New PFAS Drinking Water Rule: Ovivo Leads the Way
April 10, 2024
The EPA finalizes of Maximum Contaminant Levels (MCLs) rules for PFAS in the USA. Ovivo is leading the charge in addressing PFAS contamination challenges and ensuring safe drinking water for…
Read more
Why Water
Why Water: A Journey with Sergio Pino-Jelcic
April 9, 2024
Discover Sergio Pino-Jelcic’s inspiring journey in water treatment, sharing experiences with water scarcity and the power of biology in sustainability.
Read more
Why Water
Why Water: A Journey with Scott Gilbert
March 18, 2024
Explore the journey of Scott Gilbert, a service center manager in New York, as he shares insights from his remarkable career spanning the military to the semiconductor industry.
Read more